Plastics have grown to be an integrated section of modern production, and among the many procedures available, rotational molding—or Materials Rotational Molding —stands out as a head in making top quality, resilient, and tailored plastic products. Its rising reputation has situated it as you of the most successful solutions for industries requiring unique and complex plastic designs.
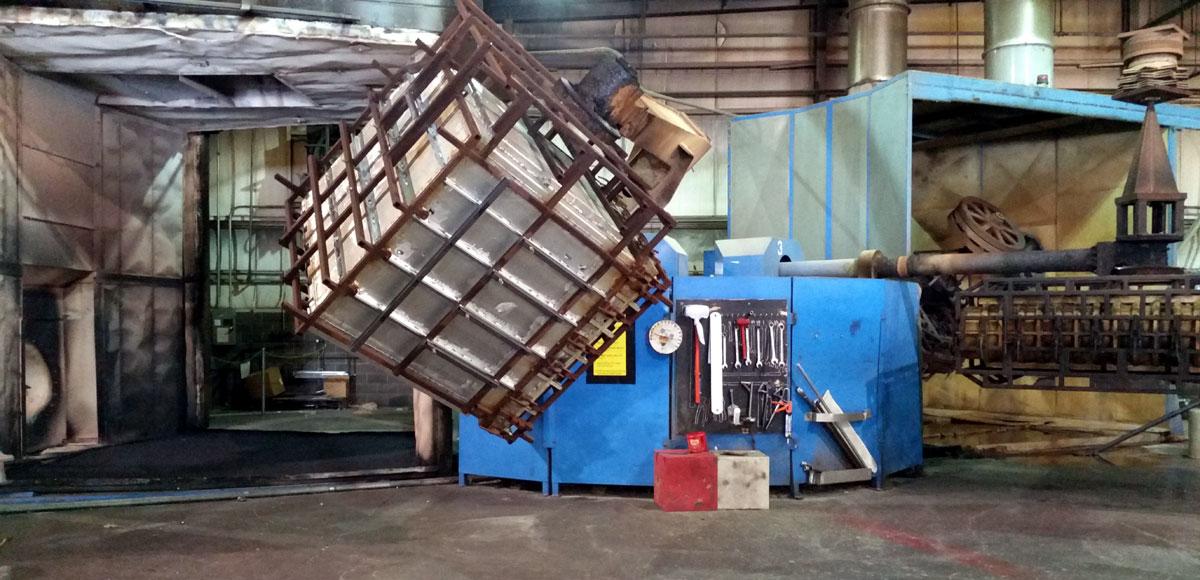
What Is Plastics Rotomolding?
Rotomolding is a production process that uses temperature and slow rotation to create hollow, smooth plastic products. Utilizing a mold full of powdered plastic resin, the procedure evenly directs material throughout the mold's interior through consistent rotation. Once cooled, the created plastic takes their ultimate form, causing powerful and very customizable products.
Unlike injection or strike molding, rotomolding doesn't count on additional pressure. This allows for larger design flexibility and the ability to develop big, delicate items without reducing architectural integrity.
Why Materials Rotomolding Is really a Top Choice
Rotomolding has attained their reputation for providing supreme quality plastic items, and there are several persuasive reasoned explanations why more industries are turning to the method.
1. Remarkable Toughness
One of many key features of rotomolding may be the power and toughness of the completed products. Plastic items produced through this process have uniform wall depth and number disadvantages or stitches, lowering the chance of breakage. This makes it ideal for programs demanding things like water tanks, outdoor furniture, and industrial-grade containers.
2. Modification Choices
With rotomolding, tailoring items to meet specific specifications is simple. From complex designs to extraordinary completes, this technique is flexible enough to accommodate special design needs. Also, companies may combine features like finishes, logos, as well as multi-layered styles without seeking extra processes.
3. Cost-Effectiveness for Minimal Volumes
Rotomolding excels in providing smaller groups and prototypes at a cost-effective cost. Since the shapes are less complex and involve little maintenance, businesses can produce custom styles without large upfront investments.
4. Eco-Friendly Potential
Rotomolding often contains recyclable resources and creates small waste throughout production. The industry's raising focus on sustainability has produced rotomolding a fitting selection for makers trying to reduce their environmental impact.
Transforming the Pockets Business
Rotomolding continues to climb in relevance across several industries, including automotive, healthcare, and agriculture. Their capacity to handle varied client requirements, along with minimal manufacturing waste and exceptional toughness, roles it as a respected manufacturing process for custom plastic solutions.
To remain prior to the opposition, industries seeking progressive and tailored purposes are leveraging the initial functions of rotational molding—ensuring another wherever performance meets quality design.